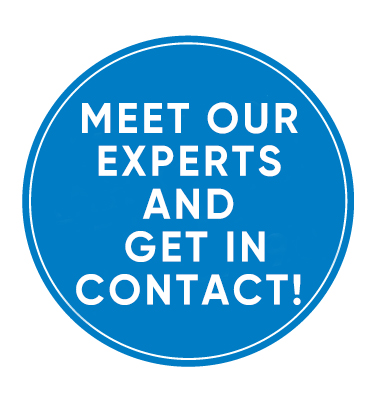
Visit us at trade fairs all around the world
We look forward to meeting you personally on our booth and enjoying interesting discussions on the subject of thermal power business.
Trade fairs 2024 - ANDRITZ Thermal Power
EVENT | LOCATION | DATE | |
London, United Kingdom | March 06-07, 2024 | ||
PulpBeyond | Helsinki, Finland | April 10-11, 2024 | MAKE AN APPOINTMENT |
Finnish Recovery Boiler Committee's 60 years' anniversary seminar | Helsinki, Finland | June 05-07, 2024 | |
ABTCP | Sao Paolo, Brazil | October 17-19, 2024 | |
Tampere, Finland | October 22-24, 2024 |
ANDRITZ Thermal Power
ANDRITZ is a leading supplier of plants based on Bubbling Fluidized Bed (BFB) and Circulating Fluidized Bed (CFB) technologies for boilers. The different technologies are distinguished by capacity, fuel, and application.
Excellent mixing and heat transfer make fluidized bed technology ideal for a wide range of applications. A variety of clean biomass fuels (bark, agricultural, forestry, and sawmill residuals) can be combusted, as well as many other fuels (demolition wood, refuse-derived fuels, peat, various sludges, etc.) and various types of waste.
Power Boilers
BFB TECHNOLOGY
In a BFB unit, the fuels are fed in above the hot fluidized bed surface. BFB systems operate at a moderately low fluidization velocity and under controlled temperature conditions. Thanks to the large heat capacity of the fluidized bed material, which is mostly sand, the combustion conditions are ideal for biomass and recycled fuels with varying moisture contents. In many installations, various fuels are fired simultaneously.
CFB TECHNOLOGY
With CFB technology, the flue gas velocity in the furnace is higher and the bed is expanded and entrained with the flow. The bed material flows with the flue gas through the furnace, after which the material is separated by cyclones and returned to the lower furnace. CFB technology also allows an extremely wide range of fuels to be fired in the same unit. The efficient mixing and relatively low combustion temperatures contribute to low emissions of carbon monoxide, hydrocarbons, and nitric oxides.
Recovery boilers
ANDRITZ chemical recovery boilers offer designs capable of maximizing the production of green energy, with minimum emissions, while also recovering chemicals efficiently for the fiberline.
ANDRITZ supplies complete chemical recovery boiler plants, typically on an EPC basis (Engineering, Procurement, and Construction of the entire system, including support structures, boiler house, and automation). Alternatively, the recovery boiler plant can be delivered as an EP project, in which case erection and installation work are performed by others. If requested, ANDRITZ is also able to deliver the “bare boiler” only, i.e. all pressure parts of the boiler. In that case, other equipment and sub-systems can be engineered in co-operation with the customer.