SMART Simulation as a part of the design flow.
In the context of Industry 4.0, “simulation” is one of the buzzwords. It is typically used in the context of process industries, for example the Pulp & Paper industry, to describe systems which model the process to virtually train operators before the actual plant is started up. But, are there new uses and new opportunities for simulation technologies?
Simulation technology has been utilized in certain industries for some time. We are all familiar with flight simulators, for example, which are used to train military and airline pilots. The simulators can be quite realistic – presenting various scenarios to trainees in a safe, virtual environment so they can learn to master critical situations.
In a similar way, ANDRITZ’s IDEAS dynamic simulator is a cutting-edge tool in pulp and paper mills. It produces an exact virtual model of the customer’s process and the operator interface. Typically, IDEAS is employed to verify control loops in a plant’s distributed control system and then as an operator training tool. The results of using simulation are well documented – faster start-ups, quicker response to process disturbances, and faster ramp-ups to full production.
In addition to this familiar use of simulation technology, what are the latest developments? One development is the extension of the IDEAS Simulator so that it can be deployed as a certified operator training system. This has been utilized at the Zellstoff Pöls mill in Austria to carry out the recurrent training required by the mill’s insurance company to certify safe operation.
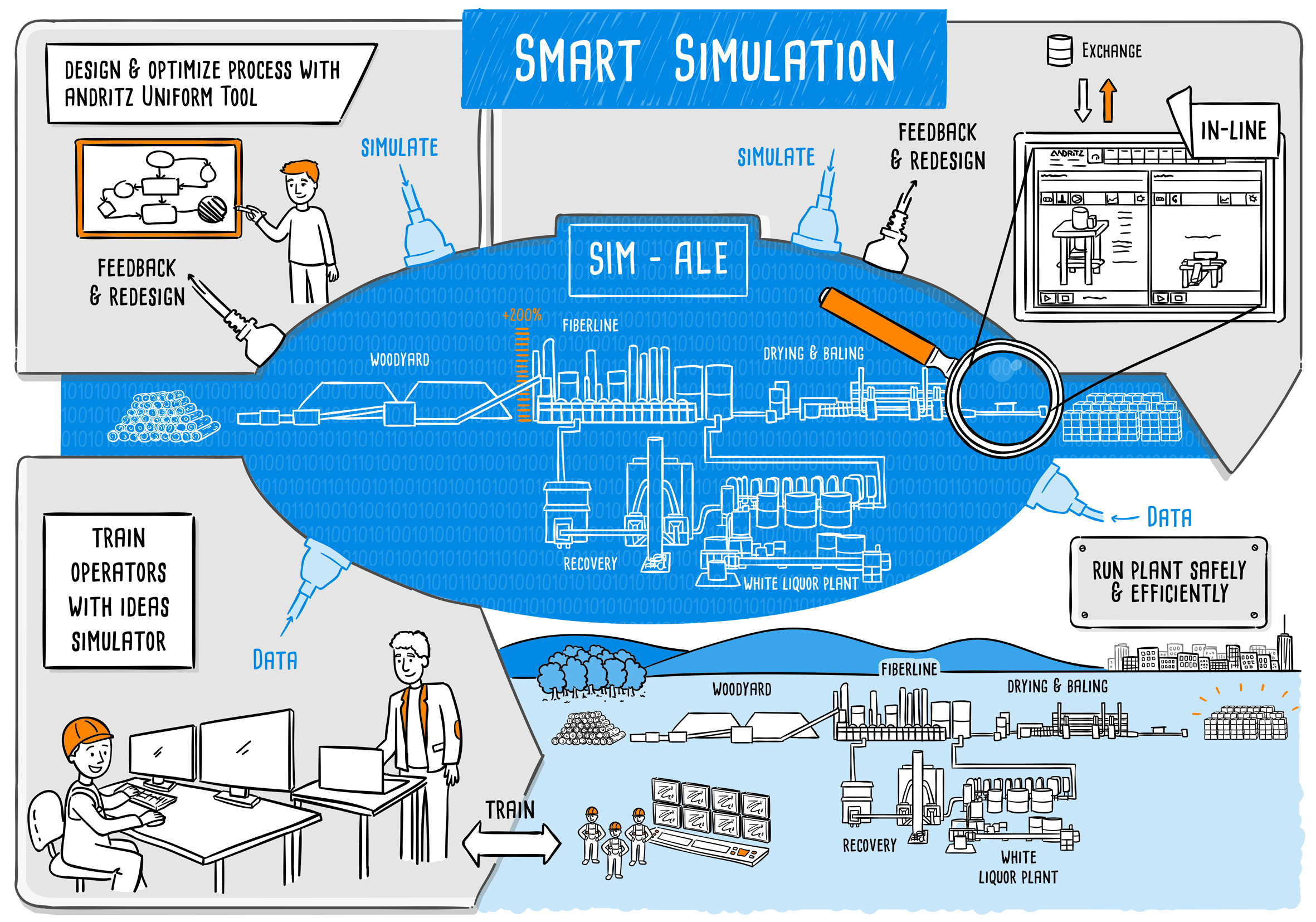
SMART SIMULATION: QUALITY ENHANCEMENT AND RISK REDUCTION
Another new development is the use of simulation technology as a design tool. For example, ANDRITZ is implementing SMART Simulation upstream in the design process to dynamically and digitally verify the design. For process design, we use the SIM-ALE platform. For machinery design, we use the IN-LINE platform.
SIM-ALE FOR PROCESS DESIGN
Within ANDRITZ, we have a common computer-assisted engineering system for process, functional, automation, and instrument design that we call the ANDRITZ Uniform Tool. In order to simulate the functional specifications being designed in this engineering tool, we developed the Simulated ANDRITZ Logic Engine (SIM-ALE) to simulate the functional behavior of the process in combination with our IDEAS system which simulates the process itself. This combination gives us the ability to verify the effectiveness of our design very early in our workflow – reducing downstream errors and expensive rework.
IN-LINE FOR MACHINERY DESIGN
With our IN-LINE simulation tool, the functional behavior of a machine is tested against the application design prior to manufacturing. This eliminates major design flaws, improves the overall quality of the machinery, and shortens the time for commissioning and start-up. The IN-LINE tool runs on virtual machines simulating the operator interface and the real machine. All of the machine’s inputs/outputs are included, as well as the actual operator interface, so that different operating scenarios (including failures) can be simulated and tested.
For example, when we apply our IN-LINE design verification tool to our bale handling machine (dried pulp bales), we can actual simulate bale transfer. All sensors and actuators are shown in the simulated user interface. A sensor or machine error can be simulated to verify how the machinery stops the bale packing process and alerts the operator. By opening the alarm screen, detailed information about how to eliminate the fault can be shown. Once this design is perfected and verified, the design is locked and passed to manufacturing for commercial release.